1. Single servo motor driven system, adopts large torque direct driven servo motor and driving unit with high overload capacity to realize low energy consumption, high transmission efficiency, reliable performance and convenient maintenance.
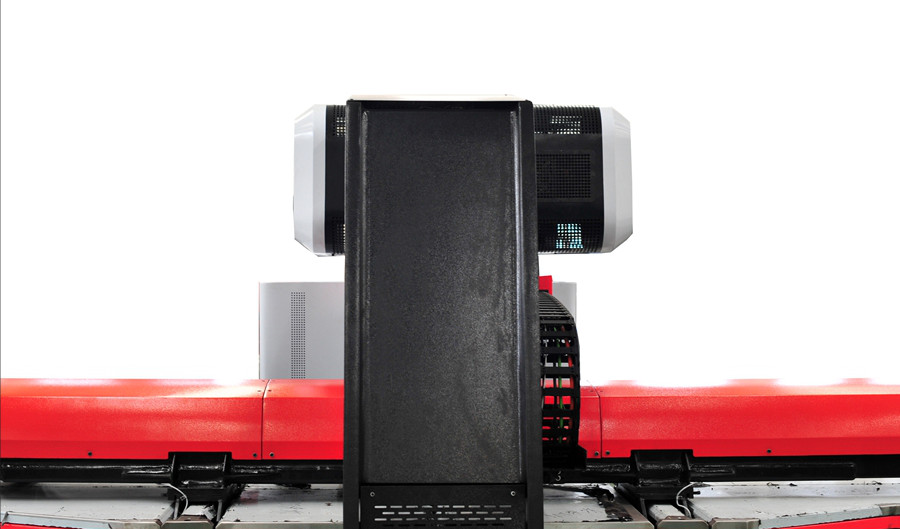
(1) Adjustable speed and stroke
a. The punch stroke can be selected according to the thickness of the sheet automatically, improving the work efficiency.
b. The punch speed is adjustable during each point of each single station,
c. the machine can realize the high speed swift during empty run and low speed during real punch, in this way, the punch quality can be improved effectively, and there is really no noise during punch.
(2). The system features with over-current protection and mechanical overload protection devices.
(3). The punch force can be automatically adjusted according to the sheet thickness and ram running speed to make the punching quality reach a high level.
2. The turret with bushing is process in pairs
The turret is processed by special device to ensure the coaxiality of the upper and lower turret and expand the service life of tooling; the bushed turret simplifies the turret structure to extend the service life; long tooling can be used to increase the guiding accuracy and expand the tooling service life (for thick sheet).
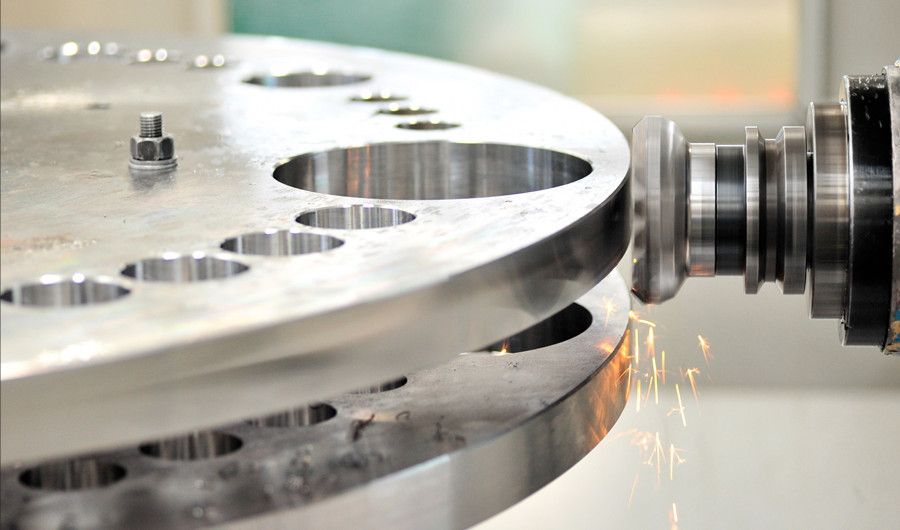
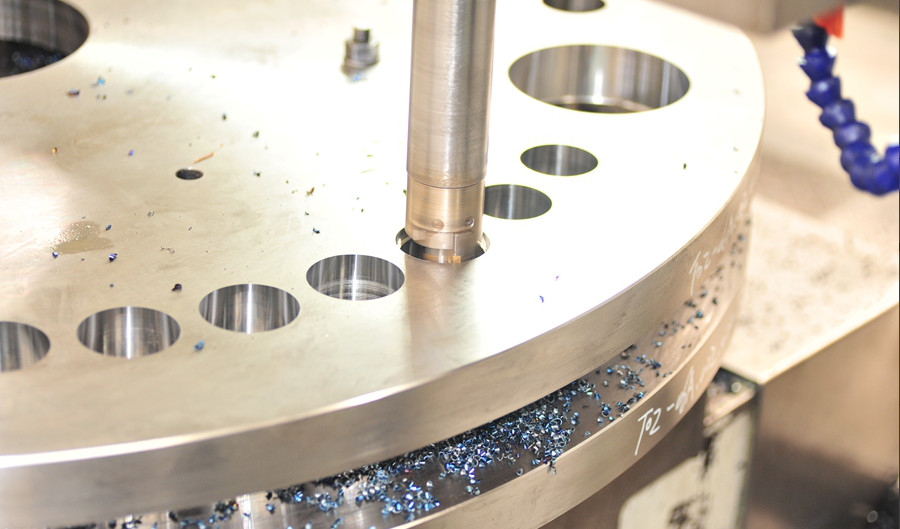
3. Imported pneumatic, lubricating and electric components ensure the reliability of the whole machine.
4. Large lead guideway and ballscrew from Japan or Germany ensures high feeding precise.
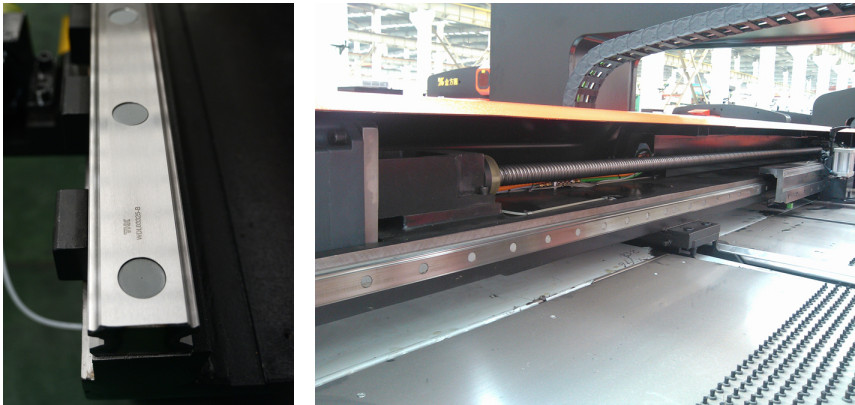
5. Hard brush and ball mixed worktable reduces the noise and vibration during running and also protects the sheet surface.
6. O-type welded frame has been vibrated for twice, the stress has been deleted completely. The frame is processed by Germany SHW dual-side pentahedron processing center at one time, no need to make second time positioning.
7. Floating clamp with large clamping force ensures the stable feeding; integrated carriage ensures good rigidity and convenient movement of clamp.
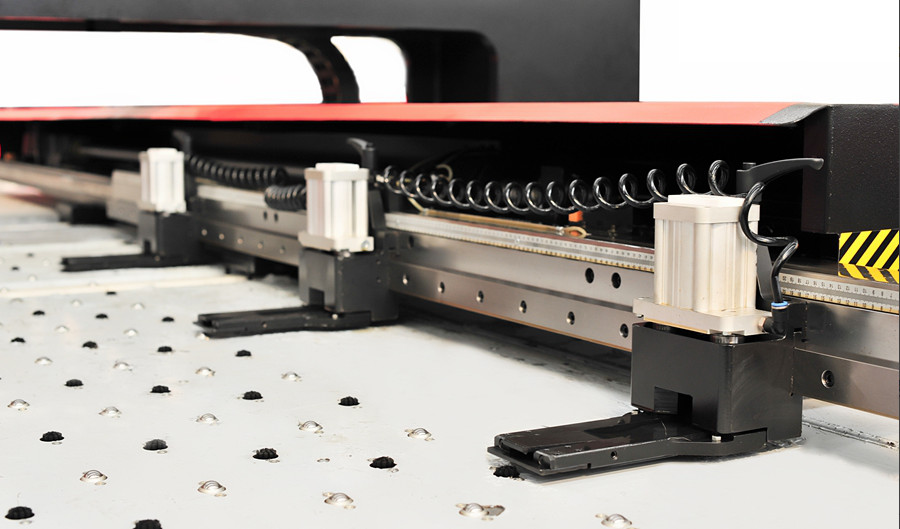
8. The system is featured with the function of automatic clamp protection to avoid the damage of tooling and clamp, ensuring the continuous running of the program.
9. The auto-index adopts high accurate worm wheel and worm mechanism, ensuring high precise indexing. The Max. tooling diameter can reach 88.9mm and the auto-index can be expanded to 4 nos.
10. Integrated beam structure to make the carriage and beam into one part, increasing the rigidity and brings the accurate positioning. The machine can run much more stably during high speed feeding and it puts an end to the deflection of X and Y axes.
11. X axis: adopts servo motor to drive the high precise balls crew and the carriage is featured with high rigidity and lightweight design. Y axis: servo motor directly drives the feeding rack which is connected with the machine guideway, split type beam is fixed with feeding rack, and the acting force will be transmitted to machine frame & ground via feeding rack and guideway in order to reduce the self vibration of the beam. This structure is featured with the characteristics of good rigidity, light in weight, low gravity, and good dynamic response in the entire feeding system, stable running and good precise.
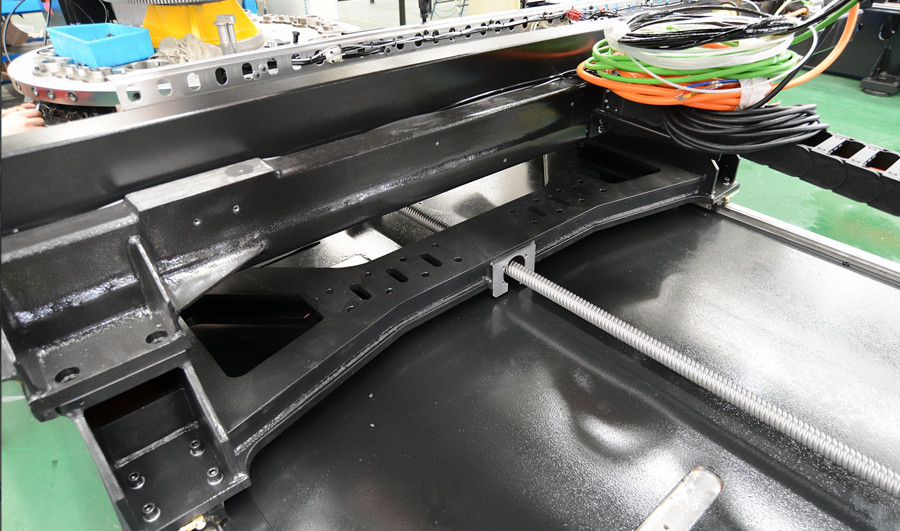
12. Central lubrication system is adopted to send the lubrication grease to the relative lubricating point directly, reducing the friction of each working pairs and increasing the service life.
13. Anti-sheet-deformation switch and sheet-anti-stripping switch are adopted.
No. | Name | Qty. | Remark |
1 | Packing List | 1 set | |
2 | Quality Certificate | 1 set | |
3 | Mechanic Operation Manual | 1 set | |
4 | Electrical Operation Manual | 1 set | |
5 | Foundation drawing | 1 set | |
6 | Electrical Principal Drawing | 1 set | |
7 | Auto-program Software System Documents | 1 set | |
8 | DBN Electrical Principal Drawing | 1 set | |
9 | Tooling manual | 1 set | |
10 | CNC system manual | 1 set | |
11 | Tooling Drawing | 1 set |
No. | Name | Gauge | Qty. |
1 | Dual-head Spanner | 5.5×7-22×24 | 1 set |
2 | Moveable Spanner | 200 | 1 no. |
3 | Socket Head Spanner | S1.5-S10 | 1 set |
4 | Cross Screwdriver | 100×6 | 1 no. |
5 | Grease Gun | HS87-4Q | 1 no. |
6 | Grease Lubrication Pump Compressor Gun | SJD-50Z | 1 no. |
7 | High pressure gun | 1 set | |
8 | T shape knob | M14×1.5 | 1 no. |
9 | Approach switch | M12 PNP SN=2 open | 1 set |
10 | Approach switch | M12 PNP SN=2 close | 1 no. |
11 | Spanner | T09-02,500,000-38 | 1 no. |
12 | Spanner for gas cylinder switch | 1 set | |
13 | Soft pipe | Ø 12 | 1 no. |
14 | Soft pipe pin | KQ2H12-03AS | 1 set |
15 | Foundation parts | 1 no. |
No. | Name | Gauge | Qty. | Remark |
1 | Clamp gear board | 3 nos. | T02-20A.000.000-10C T02-20A.000.000-24A |
|
Clamp portective board | 6 nos. | T02-20A.000.000-09C Or T02-20A.000.000-23A |
||
2 | Spring Small screw in clamp | M4x10 | 20 nos. | T02-06,001,000-02 |
M5x12 | ||||
3 | screw in clamp Inner screw | M8 x 1 x 20 | 20 no. | |
4 | Shearing blade | 30T | 2 nos. | T09-16.310,000-0.1.2 |
5 | Inner screw | M8 x 1 x 20 | 4 nos. |
FANUC CNC system is the specialized CNC system developed by Japan FANUC especially for the purpose of meet the features of this type of machine, improving the reliability of the machine to a large extent.
I、System Characteristics
1. Graphic and punch function;
2. Convenient universal G code program for easy operation;
3. Universal RS232 standard port to communicate with computer conveniently;
4. Advanced full digital servo motor and servo system;
5.10.4″ LCD colorful display;
6. Pulse encoder semi-loop feedback;
7. EMS memory: 256K;
8. Field program, office program;
9. Chinese and English display;
10. Function of graphic simulation;
11.One large capacity PCMCIA card for the backup of system parameter, ladder drawing and processing program, and realize the online process of large capacity processing program;
12. Increment in the smallest unit, position detection ad servo control to realize high speed and high accurate operation;
13. The operation button on the panel can be defined according to the real requirement;
14. Super high speed clutch data cables with little cable connection;
15. High integration, specialized software. Short time for start up, the data will not be lost if power is short of supply suddenly;
16. Storage of 400 pieces of program.
1. Linear axes: X, Y axes, rotating axes: T, C axes, punch axis: Z axis;
2. Alarm for electric error such as over- stroke.
3. Function of self-diagnose.
4. Function of soft limit.
5. Universal G code for program;
6. Function of tooling compensation;
7. Function of screw distance compensation;
8. Function of reverse gap compensation;
9. Function of coordinates deflection;
10. Function of reposition;
11. Function of AUTO, MANUAL, JOG mode;
12. Function of clamp protection;
13. Function of lock of inner register;
14. Function of parameter program;
15. Function of sub-program;
16. Function of swift positioning and punch lock;
18. Function of M code;
19. Absolute and increment program;
20. Conditioning, unconditioning jump.
Programing software introduction
We adopt CNCKAD from METALIX Company. The software is a complete set of CAD/CAM automatic programming software from design to production. With the mold library management, automatic mode selection processing, optimization of the path and other functions, can be automatically generated by the CAD drawing NC processing procedures. You can achieve a single part programming, automatic nesting and complete package.
Function of DrawingCNCKAD powerful graphics, easy and intuitive to use, in addition to the standard drawing function according to the characteristics of sheet metal, added some special drawing methods such as incision, round, triangle, right angle and contour shape, kneading, check editing and automatic correction, cutting or stamping, Chinese characters DXF/IGES/CADL/DWG file input etc..
b) Function of Punching
Featured with automatic punch, special mould, automatic indexing, automatic relocation, edge cutting, and other functions.
c) Function of Shearing
Automatic contour check and correct the parameters of the material type, thickness, single cut, cut, and shear relocation, and other functions, implementation plate automatic shear processing.
d) Post Processing
Automatic or interactive processing covers all process: stamping, laser, plasma, fire, water cutting and milling.
Advanced post processing can produce all kinds of effective NC code, support subroutine, macro program, such as optimization of tool path and the least mould rotation, support injection, vacuum suction machine functions such as material and sliding block rate.
Transfer program to another machine just need a few clicks by a mouse.These are derived from the CNCKAD post processing way, by eliminating the excessive computer files which make the operation more optimization.
e)CNC Graphical simulation
Software support any graphic simulation of CNC program, including a handwritten CNC code, editing process is also very simple, the software can automatically check for errors, such as the lost parameters clamp and distance errors, etc.
f)Transformation from NC to Drawing
Either hand written or other NC code, can be simply converted into parts graphics.
g) Date Report
Can print data report, including all information such as number of parts, processing the information such as time, mould set etc..
h) DNC Transmission
Adopting Windows interface of the transmission module, so that the transmission between PC and machine equipment is very easy.
1)、Support the current all models of CNC turret punch , laser cutting machine, plasma cutting machine and flame cutting machine and other machine tools.
2)、Support the whole process of the CNC equipment operation, including drawing, automatic or interactive processing, post processing, CNC simulation program, manual and automatic cutting, NC file download and upload etc..
3)、Can directly input Autocad, SolidEdge, SolidWork and CadKey etc including all famous CAD software generated graphics file.
4)、Software supports a variety of different numerical control equipment, can put a NC parts generate different equipment files, for multiple devices at the same time during processing.
Automatic Repositioning
When the plate size is larger than a certain range, the machine automatically re positioning, and then automatically generated positioning instructions; if the user has special requirements, can be modified or deleted on their own re positioning instructions.
Automatic clamp avoidance
Instructions generated by automatically positioning which can make the clamp avoiding dead zone, reduce the waste; whether a plate is a part or several parts of a steel plate, can realize clamp avoidance operation.
Strip material processing
In order to reduce the deformation of the material in the stamping process, the strip material processing technique can be adopted, and the cutting tool can be used in the front or the back of the branch instruction.
Pruning technique
Combined with the function of common edge punching, automatic punching which is able to punch the broken material around the edge.
Single calmp moves automatically
With a movable clamp machine can be generated by the software automatically moving clamp through NC instructions.
Minimun die rotation
The minimum die rotation option can reduce the wear of automatic indexing station and improve the production efficiency.
Function of more Punching Types
Function of triangle punching, bevel punching, arc punching and other unique and efficient punching method.
Function of Strong Auto-Punching
Automatic Punching features include automatic micro connection, intelligent selection of the mold and a wealth of alarm detection and other functions.
I) Automatic cutting function
METALIX CNCKAD contains AutoNest component which is a set of real plate automatic optimization nesting software, which can realize all the sheet metal optimization of the technical method.
1. Air supply: rated working pressure should be more than 0.6mPa, air flow: more than 0.3m3/min
2. Power: 380V, 50HZ, power fluctuate: ±5%, the electric power of 30T is 45KVA, the dynamic cable diameter is 25mm², breaker is 100A. If the power supply is not stable, the stabilizer is needed, if there is electric leakage, the protection is needed.
3.Hydraulic oil:(SHELL)Tonna T220, Or other oil for guide and rail lubrication。
Lubrication oil:00#-0# Extreme pressure grease(GB7323-94),suggestion:below 20°C use 00# Extreme pressure grease, above 21°C use 0# Extreme pressure grease
Brand | Name | Remarks | Temperature |
Shell | EPO | 0# Extreme pressure grease | 21°C above |
Shell | GL00 | 00# Extreme pressure grease | 20°C below |
3. Environment temperature: 0°C - +40°C
4. Environment humidity: relative humidity 20-80%RH(un-condensation)
5. Keep away from strong vibration or interfere of electromagnetism
6. Environment with little dust, no poisonous gas
7. Prepare the groundwork according to the foundation drawing
8. The user should select the technician or engineer for training, the educational background of whom should be at least graduated from technical secondary school, and arrange it for a long term.
11.Must prepare the foundation according to the drawing
12. A opening 65mm spanner wrench, a supporting rod afterburner, to adjust foundation level.
13. More than 5 liters of clean gasoline, a number of rags, a gun, lubricating oil, about 1 liters for scrubbing machine tools and molds.
14 with one Ф10*300 and one Ф16*300 copper rods for the mould installation. Long beam (fuselage and beam are packaged separately, but also to prepare the units shipped)
15 a dial indicator (0-10mm range), used to debug the X and Y axis perpendicularity.
16 when equipment reach the factory, prepare a 20T traffic or crane for lifting equipment
17.If V axis is equipped with water chiller motor, related cooling median must be prepared, the volume is 38L
Other matters not covered need further interpretation and coordination
CNC Turret Punch Machine;turret punch;turret punch press;cnc punching;turret punching machine;cnc punch press;cnc turret punch press;cnc turret punch;cnc punch machine;turret punch for sale;turret punch press machine;cnc punch press machine cnc punching machine for sale;cnc turret punch press machine;cnc punching and bending machine;numerical control turret punch press;servo drive turret punch press;turret punch press for sale
No. | Specification | Unit | Machine Model | ||
MT300E | |||||
1 | Max. Punch Force | kN | 300 | ||
2 | Main Driving Type | / | Single-motor driven | ||
3 | CNC System | / | FANUC CNC system | ||
4 | Max. Sheet Processing Size | mm | 1250*5000 (with one reposition) | 1500*5000 (with one reposition) | |
5 | No. of Clamp | no. | 3 | ||
6 | Max. Processing Sheet Thickness | mm | 3.2/6.35 | ||
7 | Max. Punch Diameter per Time | mm | Φ88.9 | ||
8 | Main Striker Stroke | mm | 32 | ||
9 | Max. Punch Hit at 1mm Pace | hpm | 780 | ||
10 | Max. Punch Hot at 25mm Pace | hpm | 400 | ||
11 | Max. Nibbling Speed | hpm | 1800 | ||
12 | No. of Repositioning Cylinder | set | 2 | ||
13 | No. of Station | no. | 32 | ||
14 | No. of AI | no. | 2 | ||
15 | No. of Controlling Axis | no. | 5(X、Y、V、T、C) | ||
16 | Tooling Type | / | Long Type | ||
17 | Worktable Type | / | Below 3.2mm: Full brush fixed worktable (Lifting balls for loading can be added as option) |
||
Above 3.2mm: Full balls worktable |
|||||
18 | Max. Feeding Speed | X Axis | m/min | 80 | |
Y Axis | 60 | ||||
XY Combined | 100 | ||||
19 | Turret Speed | rpm | 30 | ||
20 | Tooling Rotation Speed | rpm | 60 | ||
21 | Accuracy | mm | ±0.1 | ||
22 | Max. Load Capacity | Kg | 100/150 for ball worktable | ||
23 | Main Motor Power | kVA | 45 | ||
24 | Tooling mode | / | independent fast disassembly type | ||
25 | Air Pressure | MPa | 0.55 | ||
26 | Air Consumption | L/ min | 250 | ||
27 | CNC Memory Capacity | / | 512k | ||
28 | Clamp dead zone detection | / | Y | ||
29 | Sheet-anti-stripping Switch | / | Y | ||
30 | Anti-Sheet-Deformation Switch | / | Y | ||
31 | Outline Dimension | mm | 5350×5200×2360 | 5850×5200×2360 |
No. | Name | Brand | Gauge | ||
1 | CNC System | FANUC | OI-PF | ||
2 | Servo Driver | FANUC | AISV | ||
3 | Servo Motor (X/Y/C/T axis) | FANUC | AIS(X、Y、T、C) Special motor for V axis |
||
4 | Guideway | THK | HSR35A6SSC0+4200L (X:2500) | ||
HSR35A3SSC1+2060L-Ⅱ (Y:1250) | |||||
HSR35A3SSC1+2310L-Ⅱ (Y:1500) | |||||
5 | Ballscrew | THK | BLK4040-3.6G0+3016LC7 (X:2500) | ||
BLK3232-7.2ZZ+1735LC7T (Y:1250) | |||||
BLK3232-7.2ZZ+1985LC7T (Y:1500) | |||||
6 | Precise Bearing | NSK/Koyo | 25TAC62BDFC10PN7B/SAC2562BDFMGP4Z | ||
30TAC62BDFC10PN7B/SAC3062BDFMGP4Z | |||||
7 | Pneumatic parts | Three-joint | SMC | AC30A-03D | |
Solenoid valve | SY5120-5D-01 | ||||
Muffler | AN10-01 | ||||
Cylinder | CP96SDB40-80-A93L | ||||
8 | Electrical System | Breaker | Schneider | / | |
Contact | Schneider | / |