1.Electro-hydraulic system is adopted to control dual cylinders to get high synchronized controlling accuracy, high bending accuracy, and repositioning accuracy.
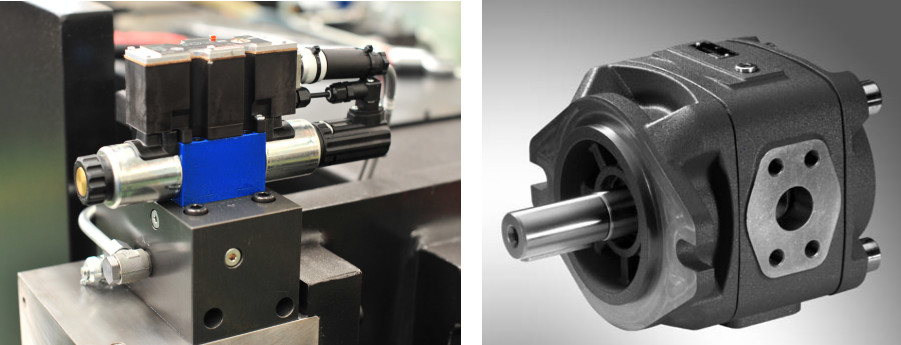
2. The mechanical deflection automatic compensation system is adopted to solve the influence of the deformation of the slider during the bending process on the quality of the workpiece. The amount of compensation is automatically adjusted by the CNC system to facilitate accuracy.
(1) The machine is compensated by a two-way adjusting structure, which can satisfy the compensation of the transverse and longitudinal direction of the machine.
(2) The dense point compensation method is adopted to make the bending accuracy more accurate.
(3) the bending of the same plate thickness material compensation once in place, different from the hydraulic compensation and back and forth movement of the structure, mechanical compensation greatly reduce the machine tool workbench fatigue deformation, improve its service life;
(4) Use special reducer and high precision potentiometer to control accurately control the accuracy of compensation.
(5) Different from the three-plate structure of hydraulic compensating worktable, this device adopts single-plate worktable design, which can effectively prevent interference in bending workpiece.
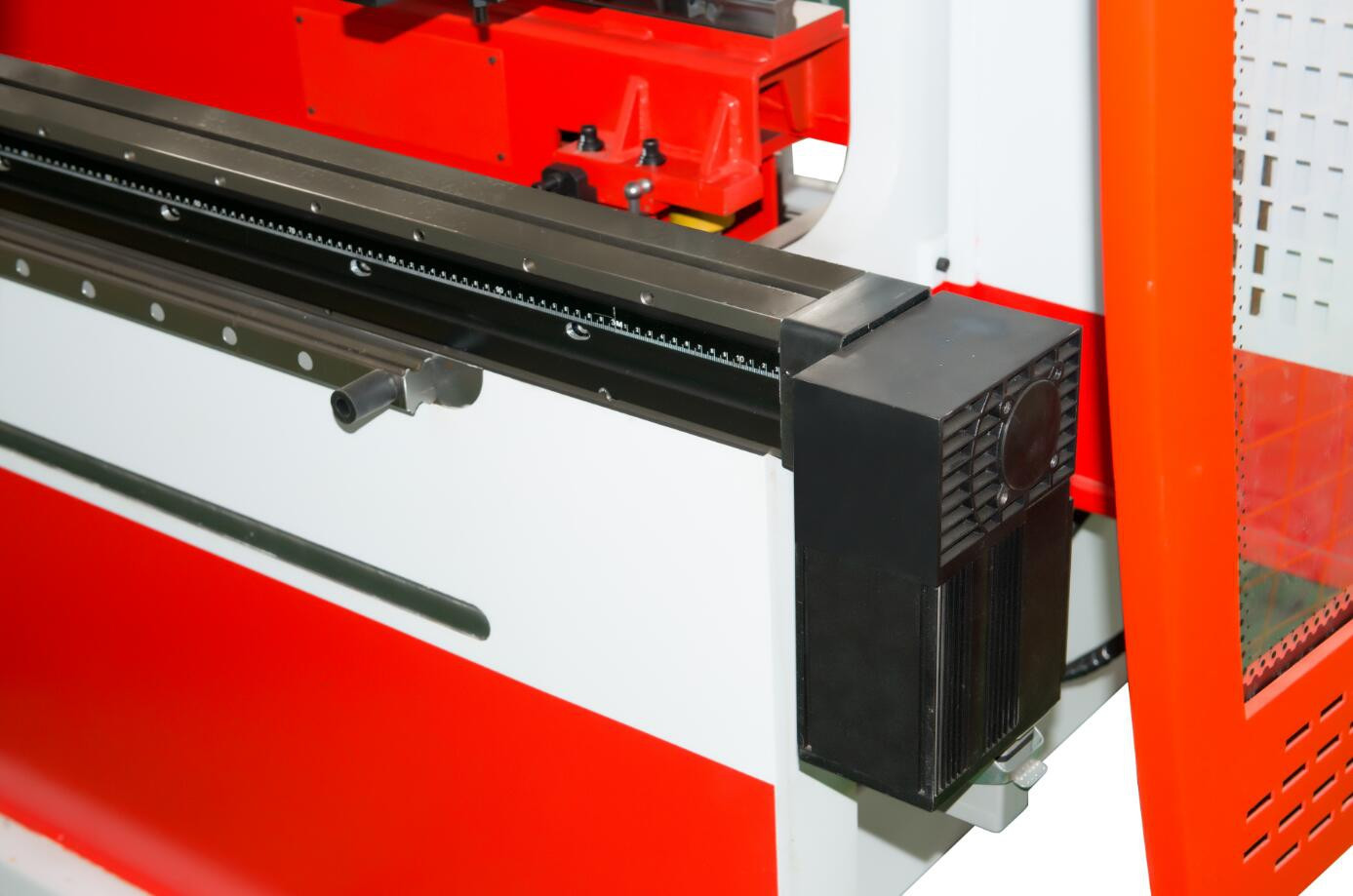
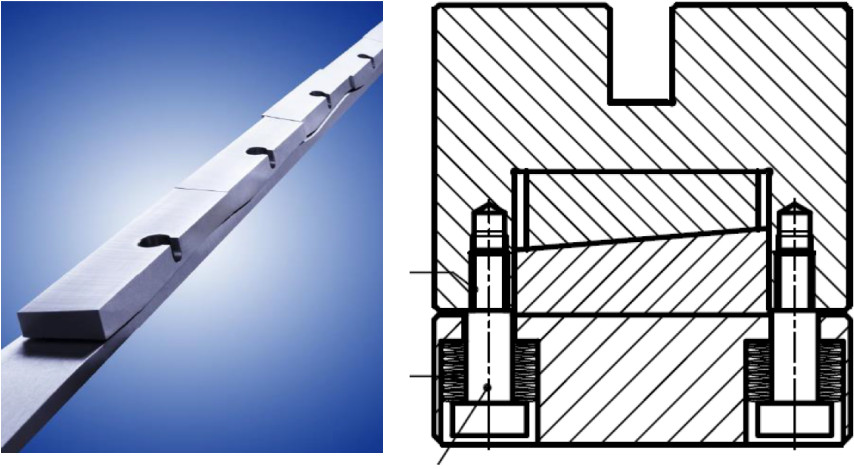
3. Multi-functional backgauge which can be expanded into 6 axes, i.e., X1 and X2 axes for back and forth, R1 and R2 axes for up and down and Z1 and Z2 for left and right. The workpiece bending can be realized flexibly.
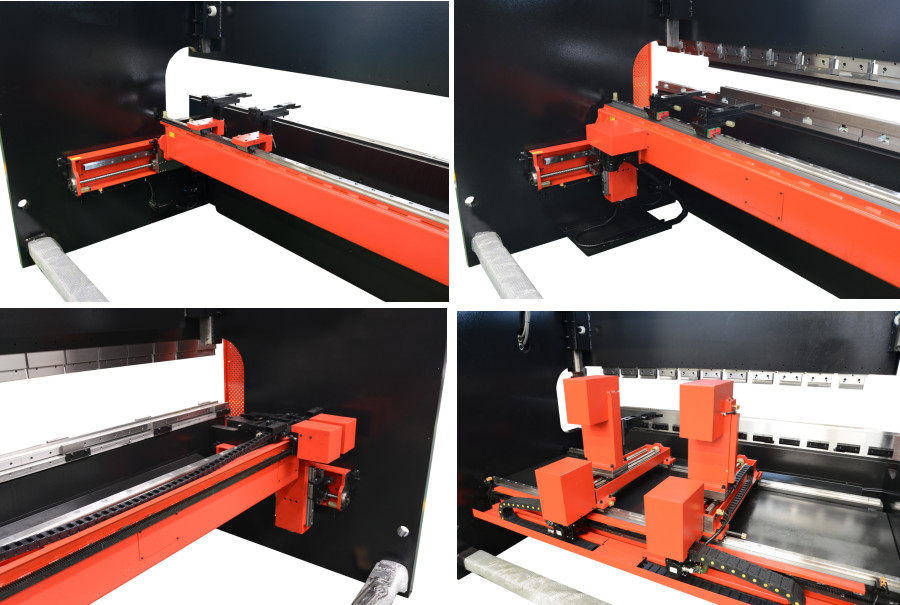
4. The frame is assembled in one time after welding, it is processed by CNC pentahedron processing center, ensuring the rigidity and processing accuracy of the frame.
5. Integrated hydraulic controlling system decreases pipeline, thus avoids oil leakage and improves the stability of performance, also the appearance of the machine is beautified.
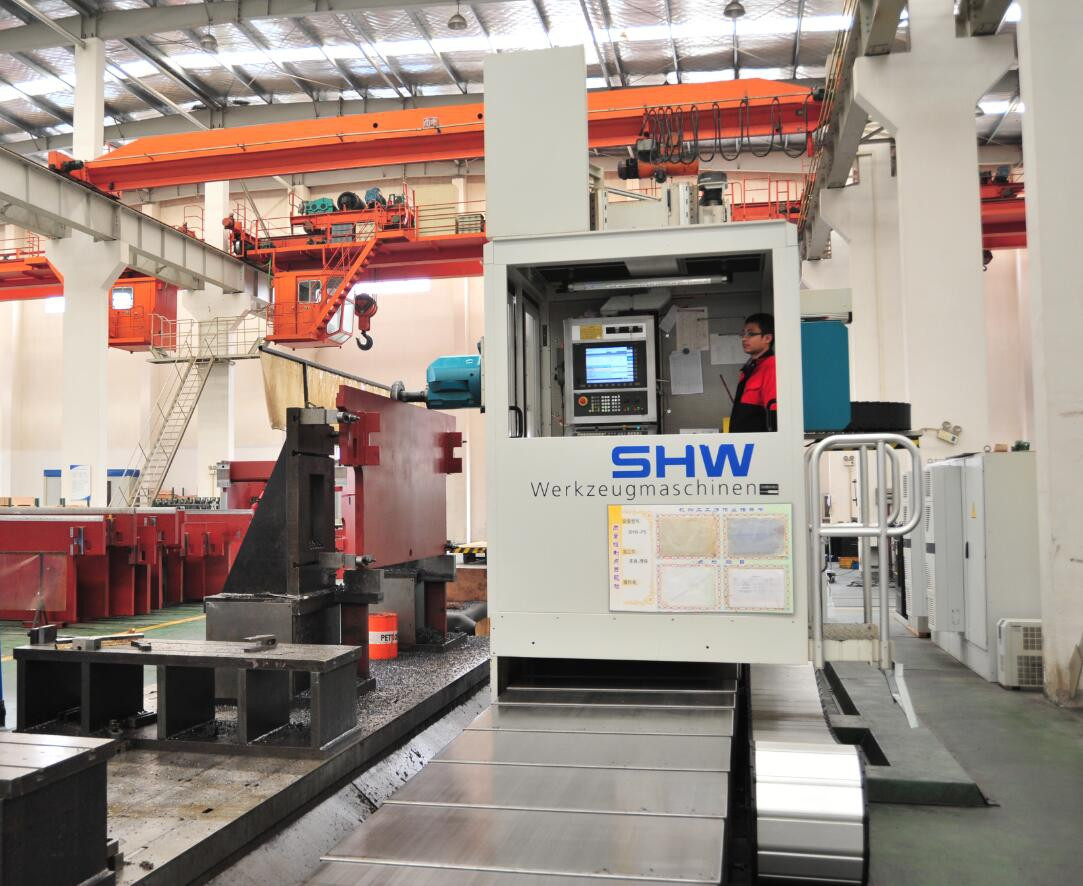
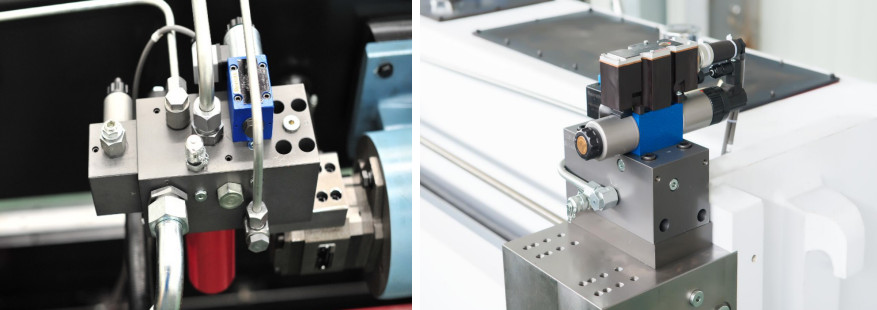
6. Segmented punch can be combined with certain length according to the bending requirement of special workpiece.
7.Hydraulic punch auto clamping or mechanic quick clamping can be equipped as option to reduce the workload and improve working efficiency.
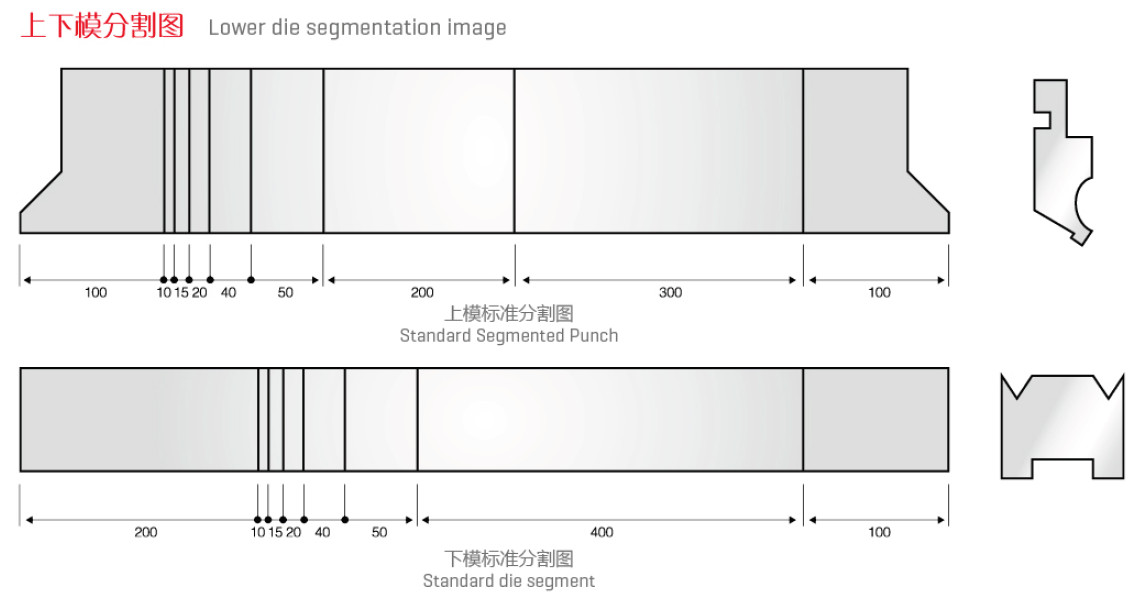
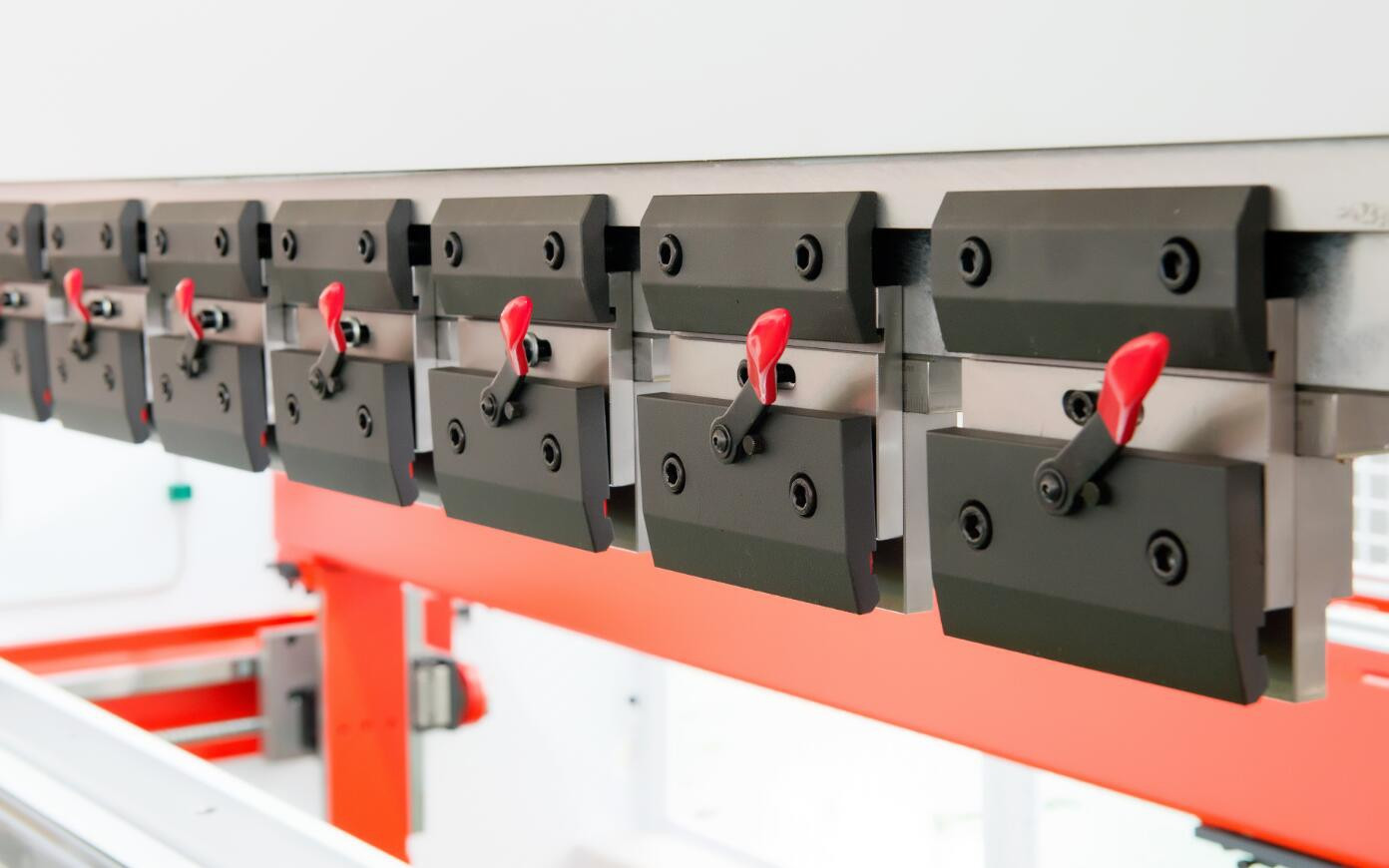
8. CNC system adopts Delem CNC system. This CNC system is featured with the latest electronic circuit, true color TFT display with high resolution ratio and multi-language menu. It is first-class controlling system for bending machine internationally.
9、The C type throat compensation device is installed under the throat of the machine tool, which is connected with the detection device. The small deformation of the bending force will not affect the measurement accuracy of the system, and the bending precision of any thickness and any material plate can be ensured.
10、Front supporter and liner guide make the movement more easiler
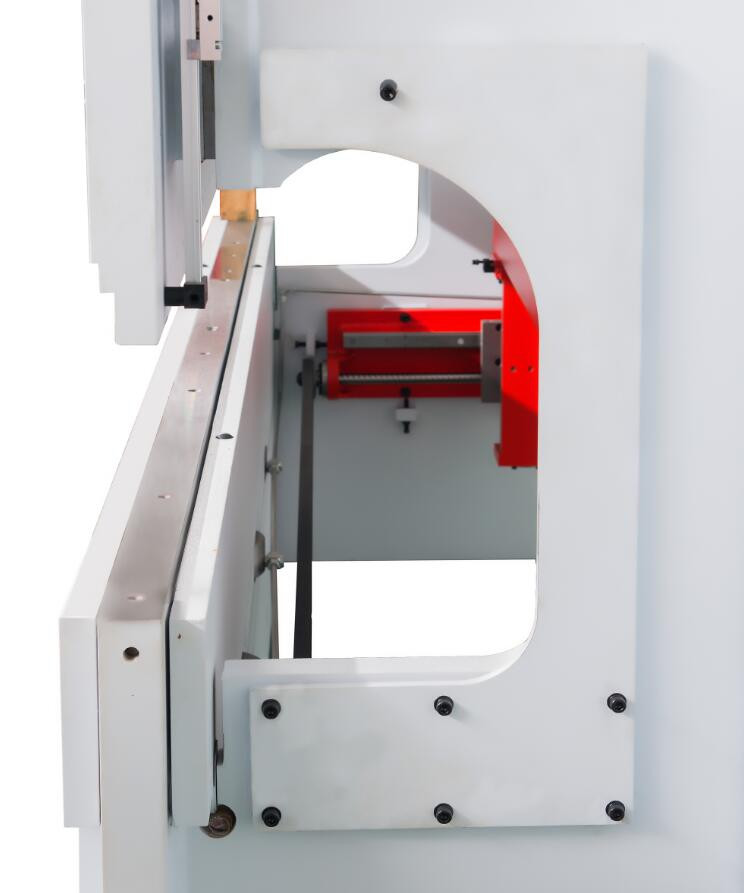
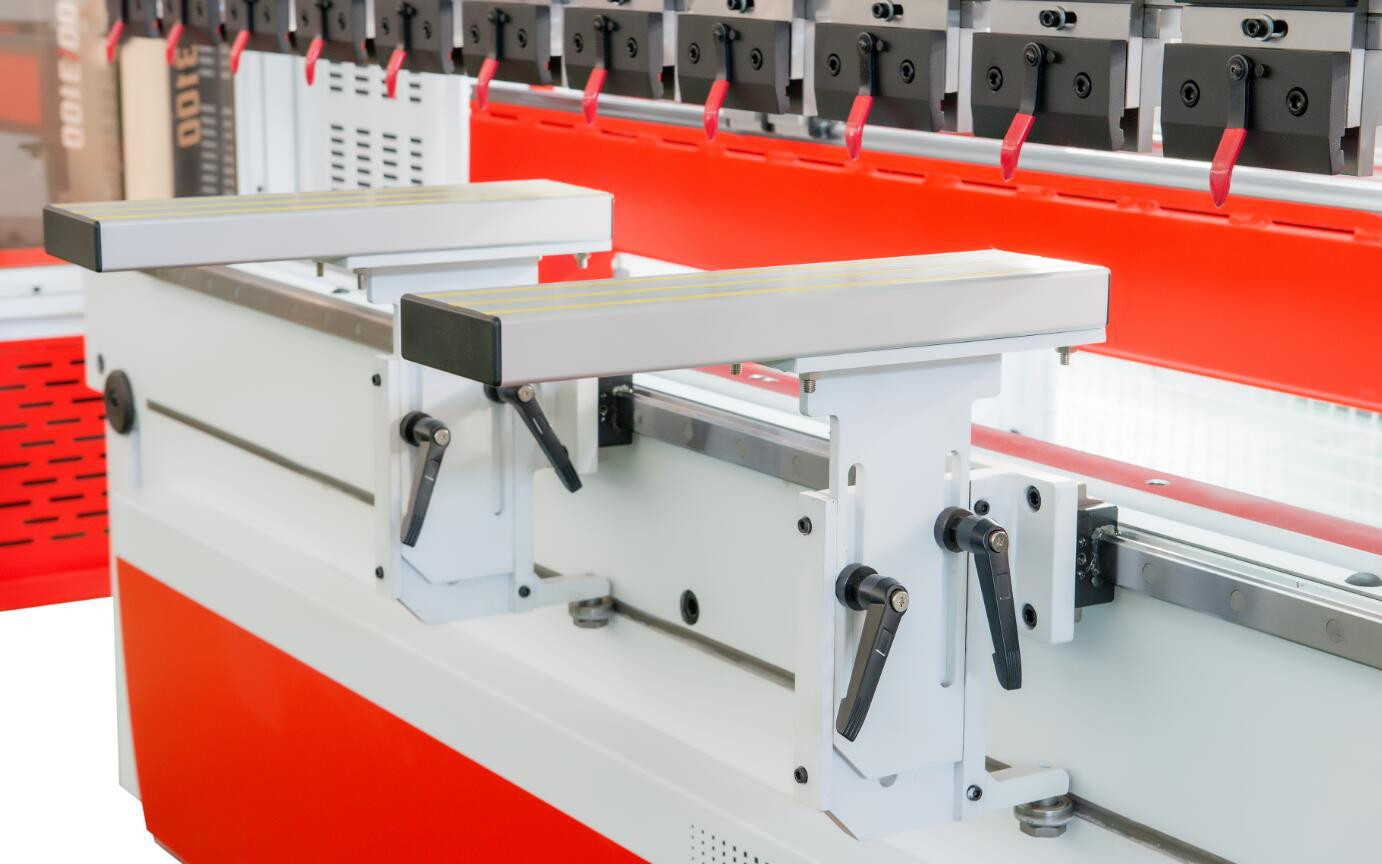
Delem DA66T CNC controlling system with internationally advanced level
1. Full WINDOWS® operation system, can realize instant machine shutdown;
2. Selection of multi languages with convenient operation;
3. Fashionable appearance design with people-oriented operation;
4. Intelligent module structure, the system can be extended into 24 axes;
5. 17 "TFT true color LCD display, 2D graphical programming;
6. Built-in PLC to reduce circuit design and increase reliability;
7. USB mouse port, keyboard port;
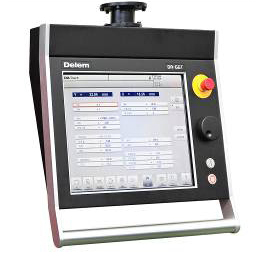
8. Auto accumulation of machine working time and bending times;
9. Bending procedure auto compilation and bending simulation;
10. Zoom free of machine appearance, tool and workpiece at the rate of 1:1:1 with graphic format;
11.Digital, graphic and other means of die programming, flat die, large arc die, multi V groove mold, variable V groove mold;
12, automatic angle correction database, self learning bending tolerance table and omni-directional collision detection function, eliminate waste products;
13. Error alarm system to avoid mal-operation;
14. Memory capacity 1G
15. Remote diagnosis;
16. Machine special analysis software, real-time monitoring;
17. Special off-line programming software can reduce programming time and increase efficiency;
18. embedded file management system, text editor;
19. Tandem operation;
20. The operation panel is equipped with emergency stop, manual moving slider and ergonomics perspective.
T-3500TCNC system
1 Use real-time WINDOWS operating system, can realize the instantaneous shutdown;
2 kinds of language options, can be set to the English interface, easy to operate;
3 fashion design, easy to operate, reflect the people-oriented;
4 standard four axis, additional modules, supports up to six axis;
5.10 "TFT true color screen, LCD touch screen, multi touch, two-dimensional graphics programming, 3D display;
6 built-in PLC function, reduce the circuit design, increase the reliability;;
7.USB mouse interface, keyboard interface;
8 automatic working hours and bending times;
9, digital and 2D graphics full touch programming, bending process 3D view, bending process automatic compiling and bending simulation;
10. Machine shape, mold and workpiece are freely zoomed in 1:1:1 according to graphics.
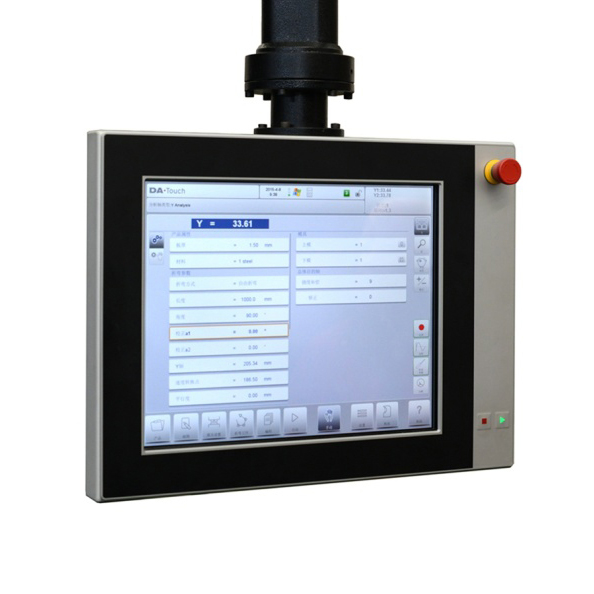
11, digital, graphic and other means of die programming, flat die, large circular arc die, multi V groove mold, variable V groove mold;
12. Error alarm system to avoid mal-operation;
13. Memory capacity 1G
14. Machine special analysis software, real-time monitoring;
15. embedded file management system, text editor;
16. Tandem operation;
17. The operation panel is equipped with emergency stop, manual moving slider and ergonomics perspective.
CNC Press Brake;cnc press brake;cnc press brake machine;cnc hydraulic press brake;cnc press brake for sale;cnc brake;hydraulic sheet metal brake;cnc hydraulic press brake machine;cnc sheet metal brake accurl press brake for sale;cnc metal brake;press brake machine;cnc hydraulic press brake bending machine;hydraulic press brake machine
Holland DELEM DA52 CNC System
1 Use real-time WINDOWS operating system, can realize the instantaneous shutdown
2. Selection of multi languages with convenient operation;
3. Fashionable appearance design with people-oriented operation;
4. Intelligent modular structure, the system can extend the 4 axis flexibly
5. 7"TFT LCD display;
6. Built-in PLC to reduce circuit design and increase reliability;
7. USB mouse port, keyboard port, RS232 port, safety PLC port;
8. Auto accumulation of machine working time and bending times;
9. Digital programming;
10. Digital mode mold programming;
11. The automatic angle correction database;
12, error warning system to prevent misoperation;
13, the memory capacity is 64M;
14, special analysis software, real-time monitoring;
15, Tandem operation;
16, the operation panel is equipped with urgent stop.
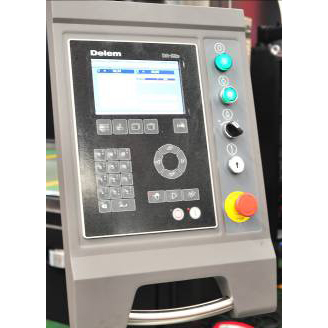
Holland DELEM DA53 CNC System
1 Use DELEM-LINUX operating system, can realize the instantaneous shutdown
2. Selection of multi languages with convenient operation;
3. Fashionable appearance design with people-oriented operation;
4. Intelligent modular structure, the system can extend the 4 axis flexibly
5. 10"TFT LCD display;
6. Built-in PLC to reduce circuit design and increase reliability;
7. USB mouse port, keyboard port, RS232 port, safety PLC port;
8. Auto accumulation of machine working time and bending times;
9. Digital touching programming;
10. Digital mode mold programming;
11. The automatic angle correction database;
12, error warning system to prevent misoperation;
13, the memory capacity is 64M;
14, special analysis software, real-time monitoring;
15. Embedded file management system, text editor
16, Tandem operation;
17, the operation panel is equipped with urgent stop.
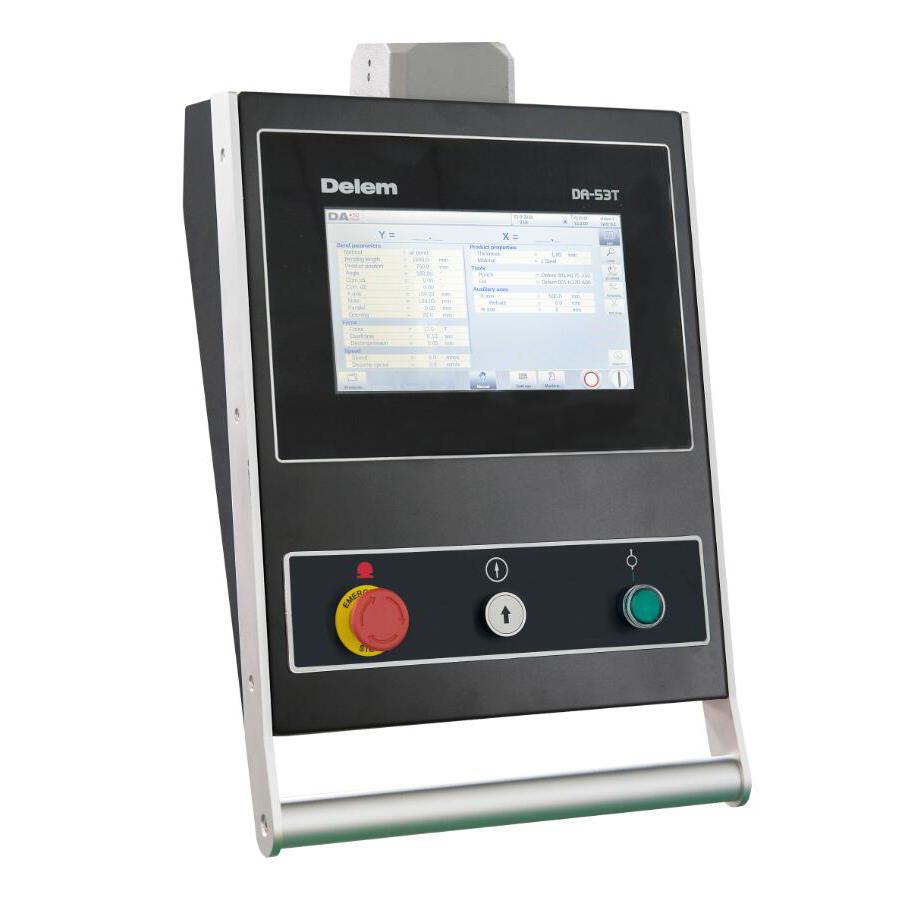
No. | Description | Quantity | Remark |
1 | Operations Files | One set | |
2 | Inner Hex Socket Spanner | One set | |
3 | Grease Gun | One no. | |
4 | Grounding Bolt | One set | |
5 | Adjusting Bolt | One set | |
6 | Foot Control | One no. | |
7 | Standard Tooling | One set |
1. Hydraulic oil: imported VG46# anti-wear hydraulic oil; and the required oil mass depend on the machine specification;
2. Power: 380V,50HZ, voltage fluctuation 10%--5%
3. Environment temperature: 0°C - +40°C
4. Environment humidity: relative humidity 20-80%RH(non-condensing)
5. Keep away from the strong vibration source and electromagnetic interference
6. Little dust, no harmful or corrosive gas
7. Prepare the foundation according to the foundation drawing
8. Select the relative personnel with certain education background for a long-term arrangement as machine operator.
No. | Description | Quantity | Remark |
1 | Operations Files | One set | |
2 | Inner Hex Socket Spanner | One set | |
3 | Grease Gun | One no. | |
4 | Grounding Bolt | One set | |
5 | Adjusting Bolt | One set | |
6 | Foot Control | One no. | |
7 | Standard Tooling | One set |
60T
Specification | Unit | PR9 060/2550 | |
Max. Bending Force | KN | 600 | |
Max. Bending Length | mm | 2550 | |
Column Distance | mm | 2150 | |
Throat Depth | mm | 350 | |
Ram Stroke | mm | 215 | |
Closed Height | mm | 530 | |
Approaching Speed | mm/s | 200 | |
Working Speed | mm/s | 18 | |
Return Speed | mm/s | 200 | |
Main Motor Power | Kw | 7.5 | |
CNC System | Holland Delem DA66T or DA52S or DA53T or T-3500T CNC system controlling Y1、Y2、X, R, Z1, Z2 axes and mechanical crowning. | ||
Oil Tank Capacity | L | 300 | |
X Axis |
Accuracy | mm | ±0.1 |
Stroke | mm | 500 | |
Speed | mm/s | 400 | |
Power | Kw | 0.85 | |
R Axis |
Accuracy | mm | ±0.1 |
Stroke | mm | 200 | |
Speed | mm/s | 200 | |
Power | Kw | 0.85 | |
Z1,Z2 Axis |
Accuracy | mm | ±0.1 |
Stroke | mm | 1250 | |
Speed | mm/s | 1200 | |
Power | Kw | 0.75 | |
Outline Dimension | Length | mm | 3400 |
Width | mm | 1400 | |
Height | mm | 2510 |
100T
Specification | Unit | PR9 100/3100 | PR9 100/4100 | |
Max. Bending Force | KN | 1000 | 1000 | |
Max. Bending Length | mm | 3100 | 4100 | |
Column Distance | mm | 2700 | 3700 | |
Throat Depth | mm | 420 | 420 | |
Ram Stroke | mm | 265 | 265 | |
Closed Height | mm | 530 | 530 | |
Approaching Speed | mm/s | 220 | 220 | |
Working Speed | mm/s | 17 | 13 | |
Return Speed | mm/s | 220 | 150 | |
Main Motor Power | Kw | 15 | 11 | |
CNC System | Holland Delem DA66T or DA52S or DA53T or T-3500T CNC system controlling Y1、Y2、X, R, Z1, Z2 axes and mechanical crowning. | |||
Oil Tank Capacity | L | 350 | 500 | |
X Axis |
Accuracy | mm | ±0.1 | ±0.1 |
Stroke | mm | 500 | 500 | |
Speed | mm/s | 400 | 400 | |
Power | Kw | 0.85 | 0.85 | |
R Axis |
Accuracy | mm | ±0.1 | ±0.1 |
Stroke | mm | 200 | 200 | |
Speed | mm/s | 200 | 200 | |
Power | Kw | 0.85 | 0.85 | |
Z1,Z2 Axis |
Accuracy | mm | ±0.1 | ±0.1 |
Stroke | mm | 1850 | 2800 | |
Speed | mm/s | 1200 | 1200 | |
Power | Kw | 0.75 | 0.75 | |
Outline Dimension | Length | mm | 3450 | 4450 |
Width | mm | 1600 | 1600 | |
Height | mm | 2750 | 2710 |
150T
Specification | Unit | PR9 150/3100 | PR9 150/4100 | |
Max. Bending Force | KN | 1500 | 1500 | |
Max. Bending Length | mm | 3100 | 4100 | |
Column Distance | mm | 2700 | 3700 | |
Throat Depth | mm | 420 | 420 | |
Ram Stroke | mm | 265 | 265 | |
Closed Height | mm | 530 | 530 | |
Approaching Speed | mm/s | 180 | 180 | |
Working Speed | mm/s | 11 | 11 | |
Return Speed | mm/s | 150 | 150 | |
Main Motor Power | Kw | 15 | 15 | |
CNC System | Holland Delem DA66T or DA52S or DA53T or T-3500T CNC system controlling X, Y1, Y2, R, Z1, Z2 axes and mechanical crowning. | |||
Oil Tank Capacity | L | 440 | 600 | |
No. of Oil Tank | no. | 3 | 4 | |
X Axis |
Accuracy | mm | ±0.10 | ±0.1 |
Stroke | mm | 500 | 500 | |
Speed | mm | 500 | 400 | |
Power | kw | 0.85 | 0.85 | |
R Axis |
Accuracy | mm | ±0.10 | ±0.1 |
Stroke | mm | 200 | 200 | |
Speed | mm | 200 | 200 | |
Power | kw | 0.85 | 0.85 | |
Z1,Z2 Axis |
Accuracy | mm | ±0.10 | ±0.1 |
Speed | mm | 1200 | 1200 | |
Stroke | mm | 1850 | 2800 | |
Power | kw | 0.75 | 0.75 | |
Outline Dimension | Length | mm | 3470 | 4470 |
Width | mm | 1720 | 1720 | |
Height | mm | 2700 | 2710 |
PR9 060
No. | Name | Model | Brand | |
1 | CNC System | DA66T/T-3500T/DA52S or DA53T CNC System | Holland DELEM | |
2 | Servo Motor | ECMA-E21315RS/SGM7G-09AFC61 | DELTA OR YASAKAWA | |
3 | Servo Driver | ASD-B2-1521-B/SGD7S-7R6A00A002 | DELTA OR YASAKAWA | |
4 | Hydraulic System | Electro-hydraulic system | Germany Bosch-Rexroth or Germany HOERBIGER | |
Synchronization controlling assembly | a. pressure valve | |||
b. active valve | ||||
c. proportional servo valve etc. | ||||
Hydraulic controlling assembly | a. cartridge valve | |||
b. proportional pressure valve | ||||
c. selector valve | ||||
d. proportional decompress valve | ||||
e. pressure valve etc. | ||||
5 | Linear guideway | 35A---760L OR 35E-760L | THK OR PMI | |
6 | Ballscrew | 25/20-1000L or R25/20-880/1000 | THK OR PMI | |
7 | Oil pump | PGH3-2X/016RE071VU2 | Germany Rexroth | |
8 | Complete set of sealing ring in oil cylinder | USA PARKER | USA PARKER | |
9 | Complete set of high pressure pipeline | 1.GE16 ZSR 3/4EDCF | USA PARKER、EO-2 pipe joint or Germany VOSS pipe joint | |
2.GE28 LR3/4EDOMDCF | ||||
3.W10 ZLCF | ||||
4.TH10 ZLR KDSCF | ||||
5.WH10 ZSR KDSCF etc. | ||||
10 | Coupling | R38 25/42 | Germany KTR | |
11 | AC contactor | LC1-D1810B7、LC1-D0910B7N etc. | Schneider | |
12 | Proximity switch | TP-SM5P2 etc. | TEND | |
13 | Terminal lead | UK2.5B、UK10N etc. | Phoenix | |
14 | Button | XB2-BVB3LC etc. | Schneider | |
15 | Painting | Holland SIKKENS | ||
16 | Crowning | National brand( standard) | SREE/UNION | |
17 | Crowning | Imported(option) | VILLA | |
18 | Front supporter | standard | JFY |
PR9 100
No. | Name | Model | Brand | |
1 | CNC System | DA66T or DA52S or DA53T or T-3500T CNC System | Holland DELEM | |
2 | Servo Motor | ECMA-E21315RS/SGM7G-09AFC61 | DELTA OR YASAKAWA | |
3 | Servo Driver | ASD-B2-1521-B/SGD7S-7R6A00A002 | DELTA OR YASAKAWA | |
4 | Hydraulic System | Electro-hydraulic system | Germany Bosch-Rexroth or Germany HOERBIGER | |
Synchronization controlling assembly | a. pressure valve | |||
b. active valve | ||||
c. proportional servo valve etc. | ||||
Hydraulic controlling assembly | a. cartridge valve | |||
b. proportional pressure valve | ||||
c. selector valve | ||||
d. proportional decompress valve | ||||
e. pressure valve etc. | ||||
5 | Linear guideway | 35A-760L OR 35E-760L | THK OR PMI | |
6 | Ballscrew | 20/25-880/1000 OR R25/20-880/1000 | THK OR PMI | |
7 | Oil pump | PGH4-3X/032RE071VU2 | Germany Rexroth | |
IPVAP5-32 | Germany VOITH | |||
HQI3-32 | Germany Eckerle | |||
8 | Complete set of sealing ring in oil cylinder | USA PARKER | USA PARKER | |
9 | Complete set of high pressure pipeline | 1.GE16 ZSR 3/4EDCF | USA PARKER、EO-2 pipe joint or Germany VOSS pipe joint | |
2.GE28 LR3/4EDOMDCF | ||||
3.W10 ZLCF | ||||
4.TH10 ZLR KDSCF | ||||
5.WH10 ZSR KDSCF etc. | ||||
10 | Coupling | R38 25/42 | Germany KTR | |
11 | AC contactor | LC1-D1810B7、LC1-D0910B7N etc. | Schneider | |
12 | Proximity switch | TP-SM5P2 etc. | TEND | |
13 | Terminal lead | UK2.5B、UK10N etc. | Phoenix | |
14 | Button | XB2-BVB3LC etc. | Schneider | |
15 | Painting | KAILEDI | ||
16 | Crowning | National brand( standard) | SREE/UNION | |
17 | Crowning | Imported(option) | VILLA | |
18 | Front supporter | standard | JFY |
PR9 150
No. | Name | Model | Brand | |
1 | CNC System | DA66T or DA52S or DA53T or T-3500T CNC System | Holland DELEM | |
2 | Servo Motor | ECMA-E21315RS/SGM7G-09AFC61 | DELTA OR YASAKAWA | |
3 | Servo Driver | ASD-B2-1521-B/SGD7S-7R6A00A002 | DELTA OR YASAKAWA | |
4 | Hydraulic System | Electro-hydraulic system | Germany Bosch-Rexroth | |
Synchronization controlling assembly | a. pressure valve | |||
b. active valve | ||||
c. proportional servo valve etc. | ||||
Hydraulic controlling assembly | a. cartridge valve | |||
b. proportional pressure valve | ||||
c. selector valve | ||||
d. proportional decompress valve | ||||
e. pressure valve etc. | ||||
5 | Linear guideway | 35A-760L OR 35E-760L | THK OR PMI | |
6 | Ballscrew | 20/25-880/1000 OR R25/20-880/1000 | THK OR PMI | |
7 | Oil pump | PGH4-3X/032RE071VU2 | Germany Rexroth | |
IPVAP5-32 | Germany VOITH | |||
HQI3-32 | Germany Eckerle | |||
8 | Complete set of sealing ring in oil cylinder | USA PARKER | USA PARKER | |
9 | Complete set of high pressure pipeline | 1.GE16 ZSR 3/4EDCF | USA PARKER、EO-2 pipe joint or Germany VOSS pipe joint | |
2.GE28 LR3/4EDOMDCF | ||||
3.W10 ZLCF | ||||
4.TH10 ZLR KDSCF | ||||
5.WH10 ZSR KDSCF etc. | ||||
10 | Coupling | R38 25/42 | Germany KTR | |
11 | AC contactor | LC1-D1810B7、LC1-D0910B7N etc. | Schneider | |
12 | Proximity switch | TP-SM5P2 etc. | TEND | |
13 | Terminal lead | UK2.5B、UK10N etc. | Phoenix | |
14 | Button | XB2-BVB3LC etc. | Schneider | |
15 | Painting | KAILEDI | ||
16 | Crowning | National brand( standard) | SREE/UNION | |
17 | Crowning | Imported(option) | VILLA | |
18 | Front supporter | standard | JFY |
CNC Press Brake;cnc press brake;cnc press brake machine;cnc hydraulic press brake;cnc press brake for sale;cnc brake;hydraulic sheet metal brake;cnc hydraulic press brake machine;cnc sheet metal brake accurl press brake for sale;cnc metal brake;press brake machine;cnc hydraulic press brake bending machine;hydraulic press brake machine