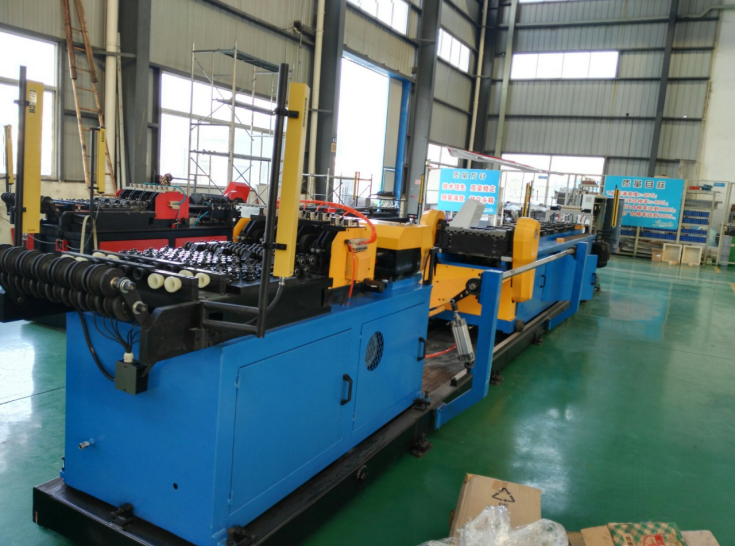
1、Structure: Servo length fixing and return material, hydraulic system using constant rate vane pump, swing cylinder drive bending. The machine is composed of the material rack, the cutter and the bender, and the bender moves in the length direction to realize the production of the workpiece with different length. Automatic cycle: straighten → feed → compact → cut → bend → pull core → release → discharge → reset.
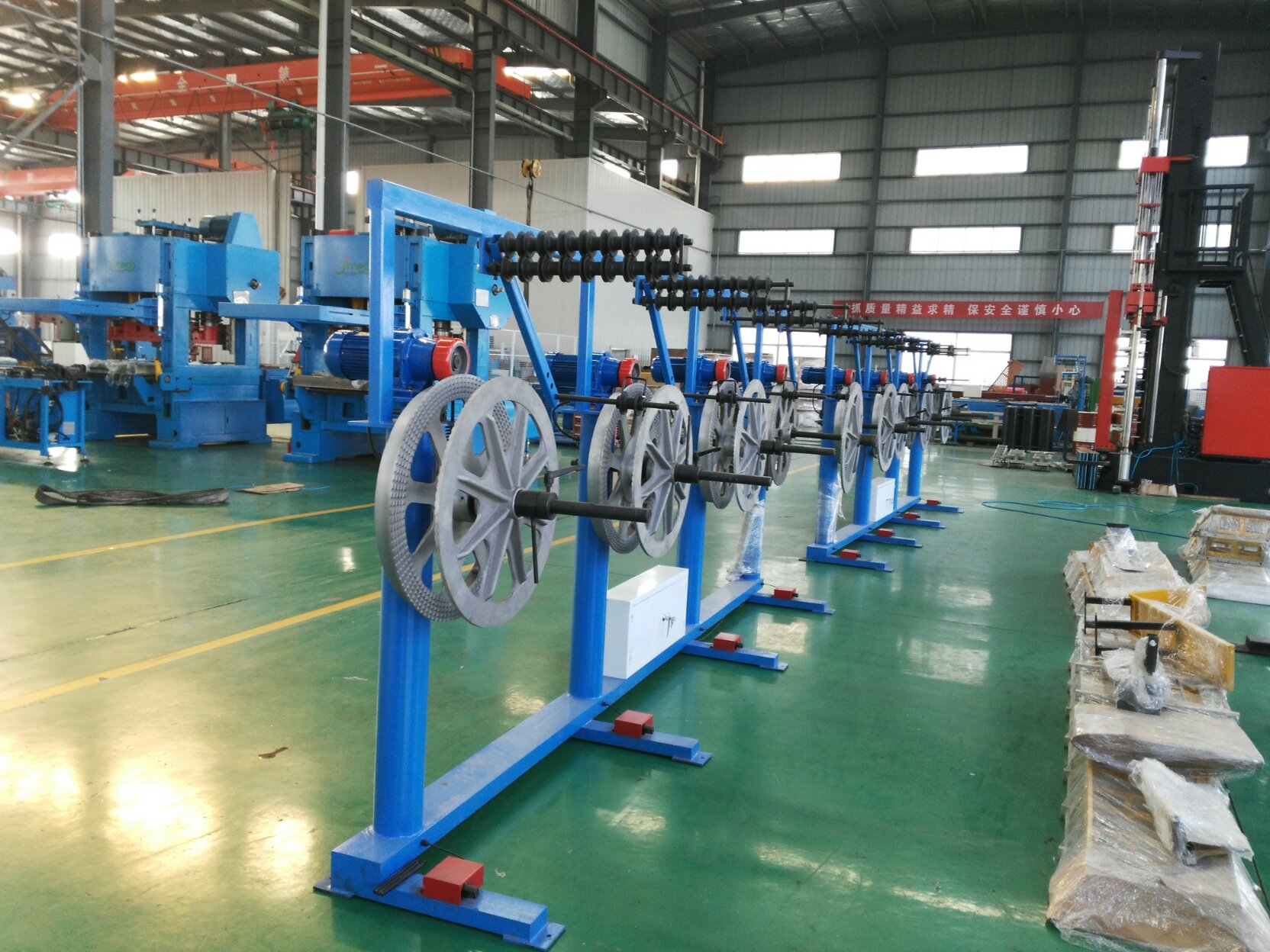
Electric drive de-coiler rack, aluminum alloy tray (load capacity ≤ 150Kg).
Rack(inside pumping type)
3、Straightening device: the alignment wheel is arranged in the horizontal and vertical surface, it rounding and straightening the cooper tube from two sides, each copper tube has four rounding wheels and 12 alignment wheels, which 1 rounding wheel and 4 alignment wheels through the eccentric shaft adjustment, in order to ensure the straightness of hairpin tube.
4、Short of Material detection: the use of photoelectric switch detection, arranged in front of the alignment wheel.
5、Feeding device: use of friction feeding, the structure is the cylinder presses the belt with feed. Each set of synchronization belt with a separate cylinder, feeding cylinder press timing belt, the upper and lower timing belt clamping a copper tube friction feeding, when feeding in place, the feed speed slower down, timing belt pressing cylinder pressure lower down as well, which cooper tube in place, its squeezed cylinder lost pressure, in order to avoid the cooper friction to deformation. Hydraulic oil motor drive feed, high and low speed hydraulic valve easy to achieve by the slow (starting) → fast → slow (in place) the work of the beat to ensure high efficiency and the quality of the workpiece.
6、Feed in place with the sensor switch detection.
7、 Cooper tube cutting device: use of external hob cutting cooper tube, cutting spray fog lubrication, each cooper tube cutting depth can be adjusted separately to ensure that the copper pipe cutting synchronization, shrinkage less, after cutting , the feed belt reverse to separate the cooper tube.
8、 Bending device: composed by the bending clamping, bending rotation, bending mold up and down and other parts. To ensure reliable clamping when bending, one cooper tube with one bending mold, each bending mold with a clamping cylinder. The bending rotary device is rotated by the swinging cylinder driven by the bending device. The bending mold is mounted on the fixed plate driven by two cylinders. When the mold is lowered, it can be fed or unloaded. When the template is raised, the bending mold is completed the bending.
9、Discharging, core pulling, and mandrel device: the above devices are installed on the rail. After the bending of the copper pipe is completed, the movable mandrel is driven by the cylinder in the bending mode clamping state, exits the bending cut point, and then discharges. The servo motor through the ball screw drive the unloading seat to move forward quickly, The connection with the movable mandrel is a connecting rod made of thick-walled cold drawn seamless pipe with oil mist lubricator and dispenser, through the distributor and the holes in the connecting rod to spray in the inner wall after the mould clamps the cube and bending to ensure the quality of the elbow.
10、Clamp length adjustment device: if the hairpin length specifications changes, it should be adjusted by length adjustment device, length adjustment device has the following parts.
① bending length adjustment: used to adjust the length of the workpiece after bending, the discharge seat positioning derived by the servo motor through the ball screw; bending machine positioning completed by the servo motor drive screw, when it is in place, the automatic clamping device and the base fixed.
② Guide rack, feeder adjustment device: According to the hairpin tube different lengths, the equipment is equipped with different length of the guide rack. The feeder is driven by the cylinder, the receiving arm is mounted on a long shaft, and the receiving arm can slide along the long axis, change the distance between the picking arms, or increase the number of picking arms to meet the different lengths of the workpiece picking up.
11、Machine equipped with safety photoelectric protection devise on both sides of the equipment.
12、Hydraulic station arranged in cutting frame, it is used of constant rate vane pump with air cooler.
S.N. | Content | Brand/Origin |
1 | PLC | Mitsubishi |
2 | Man machine interface | Mitsubishi |
3 | Servo Motor | Mitsubishi |
4 | Pneumatic solenoid valve | SMC |
5 | Cylinder | SMC |
6 | Hydraulic components | YUKEN/Japan |
7 | Eclectics components | Schneider |
8 | General motor | Joint brand |
9 | Reducer | Joint brand |
10 | Bearing | C&U/NSK |
11 | Linear guide | HIWIN |
Item | Parameter | ||||
Model | ZUXB 4-9.52×25.4+4-12.7×48-3600-ACD | ||||
A. Electric discharge B. Inside pumping discharge C. Pneumatic arm discharge D. Photoelectric protection device |
|||||
Cooper Tube | Material | Material | Alloy code: TP2(soft)(Meet GB/T 17791Standard) | ||
Type | Max. outer diameter Φ1100mm | ||||
Thickness mm | 0.3~0.41(Suggested) | ||||
OD mm | Φ9.52 | Φ12.7 | |||
Work piece size | Center distance mm | 25.4 | 48 | ||
Max. length mm (Minimum 200) |
3600 | 3600 | |||
Processing number at the same time | 8 | ||||
Automatic machining cycle s/time |
≤14(calculates at 1m workpiece) | ||||
Electrical specifications | Power supply | AC380V/50Hz, ±10%。 | |||
Oil pump motor power | 1.5 kW | ||||
Cutter motor power | 1.5 kW | ||||
Feeder motor power | 3KW | ||||
Bending motor | 2kW Servo motor | ||||
Fixing length motor | 0.4 kW Servo motor | ||||
Hydraulic | Hydraulic pump | constant rate vane pump | |||
Hydraulic oil | ISOVG32/hydraulic tank capacity 160L | ||||
Work pressure | ≤6.3MPa | ||||
cooling way | Air cooling | ||||
Air supply | 0.4~0.6MPa, 500L/min | ||||
Volatile oil | Japan Idemitsu KosanAF-2C/ oil tank capacity20L |